FEATURE STORY
Game Changer Part II: Northrop Grumman and the James Webb Space Telescope’s Confounding Sunshield
By David Larter

From day one, everyone involved in the program knew that when NASA’s James Webb Space Telescope (Webb) arrived on orbit it would change humanity’s understanding of our cosmic origins.
If it worked.
First, the only deployable, passively cooled infrared observatory – with its delicate, tennis court-sized sunshield – had to unfold in space en route to its destination a million miles from earth – beyond any manned rescue mission.
No one had ever attempted anything like it.
Its predecessor, the Hubble Space Telescope, was robotically extracted from the mission bay of the Space Shuttle Discovery in 1990. Hubble was constructed as a 27,000-lb. monolithic spacecraft with a 2.4-meter optic. Webb would be more like a transformer, the fictional alien robot cars: a 14,300-lb observatory with a 6.5-meter optic that would go from stowed inside a 5.4-meter-diameter rocket fairing atop an Ariane 5 and morph into a 21 m x 14 m (69.5 ft. x 46.5 ft.) final spacecraft.
Designing a lightweight observatory with moving parts and pieces that could survive launch, then deploy in space and operate and cryogenic temperatures, presented a mountain of challenges for the team at Northrop Grumman, said Josh Levi, a test and integration engineer who has worked on the program almost from the beginning.
“When you want to survive launch, you want to make the telescope really stiff so it doesn’t move around and tear itself up as it’s getting to space,” Levi recalled from his Space Park office in Redondo Beach. “And when you want to it to be deployable, you need to have gaps, hinges, and other things like that which are going to vibrate and potentially break during launch. And then when you want to operate at cryogenic temperatures you have you have to use soft materials that can expand in predictable ways.”
All those requirements compete with each other, Levi said, and that made the design incredibly complex.

While everything about Webb was challenging to design and build, perhaps no part of the program better exemplifies the observatory’s intricacy and innovation as does its five-layered, deployable sunshield.
The story of how Northrop Grumman, collaborating with of NASA and industry partners, designed and built the first-of-its-kind sunshield represents just one of the groundbreaking innovations that makes Webb a marvel of engineering. But its journey from a rough concept to its triumphant deployment in space is an exemplar of innovation and overcoming daunting challenges, one step at a time, to define possible.
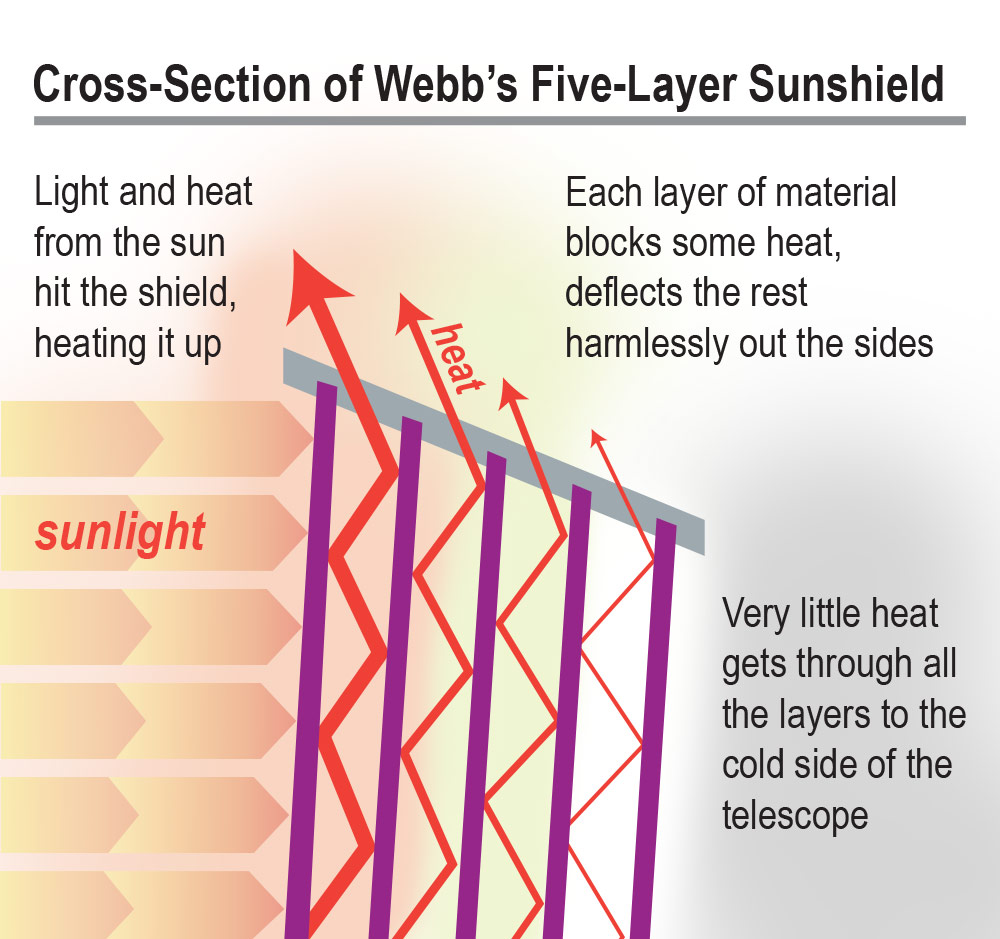
The basic idea behind the sunshield is this: A giant, kite-like structure of five layers that both blocks the light and heat radiating from sun and earth. Additionally, it vents heat generated by Webb’s onboard electronics into space to prevent it interfering with Webb’s infrared images. To capture light from the first stars and galaxies, Webb’s instruments must be as cold as possible.
Each layer of the sunshield is cooler than the previous layer, with the outermost layer – the first line of defense from the sun’s baking heat – reaching temps up to 185 degrees Fahrenheit. By the time the heat reaches the last layer, it has dropped by about 573 degrees Fahrenheit, allowing the observatory’s instruments to operate below 40 degrees Kelvin or about -388 Fahrenheit.
The challenges were legion: The team had to build a deployable structure at a level of complexity never previously attempted that could survive launch, block nearly all heat radiating from the sun and earth to prevent it from interfering with Webb’s infrared instruments, and do all of that without being able to simulate on-orbit conditions on a full-scale model – no such facilities exist.
NASA’s Webb program focused on maturing new technologies early, retiring those technical risks over a year prior to what’s known as a preliminary design review – an early check between the agency and industry to make sure the design is on track. What remained were the engineering challenges that come with many “firsts,” such as the sunshield, which would be worked out later in the program.
From the get-go, everyone knew accomplishing the sunshield’s innovative deployment sequence would be hard. But since the deployment architecture didn’t require any from-scratch inventions to make it work, the heavy development work for it was scheduled for a little later in the program, said Charlie Atkinson, Northrop Grumman’s chief engineer for Webb.
“All the things that weren’t mature technologies with demonstrated past performance got the attention early,” Atkinson said. “The sunshield’s deployment was based upon demonstrated technology, so it didn’t really fall into that category. It was just really hard engineering as opposed to new technology.
Membrane Material
During the first six years of the program, NASA, Northrop Grumman, and their industry partners pushed ahead on the primary mirror’s hexagonal beryllium mirror segments, the sophisticated backplane that would hold them in place and mount the actuators for adjusting and alignment, the telescope and its alignment process, and the many technologies needed for the scientific instruments.
On the sunshield, the membrane material itself was considered one of Webb’s new technologies, so the NASA/Northrop Grumman team got to work on it early.
The perfect sunshield membrane material would need to:
- Survive folding up for stowing and unfolding for deployment;
- Stand up to the unique radiation environment at Lagrange Point 2, where Webb would live for the duration of its mission;
- Reduce the impact of micrometeoroids; and
- Hold a coating that can reflect the light back into space and be feasibly produced at the scale needed for 5 tennis-court sized soft structure layers.
The team chose Kapton E. Manufactured by DuPont, a tough film about as thick as a human hair that the team found to have the right characteristics to stand up to the harsh environment of space, maintaining a stable shape over the range of temperatures it would encounter on orbit.
The Kapton E would then be coated with semi-conductive silicon and vapor-deposited aluminum, which reflects the sun’s energy back into space. The coatings on sunshield’s five membrane layers reduce the sun’s energy from 250,000 watts when it hits the first layer to a single watt by the time it reaches the last layer.
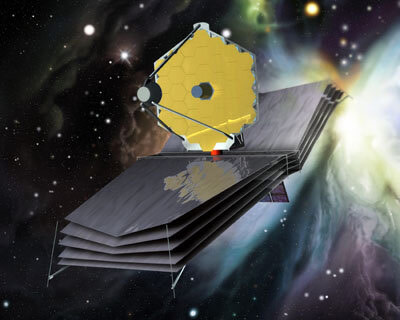
Taking Shape
Even as the heavy lifting on the sunshield architecture was pushed to later in the program by design, the teams made steady progress on it. When Jim Flynn, Northrop Grumman’s sunshield manager, first joined the program in 2004, the company had a team of four working on maturing the concept first developed by NASA.
“The team had an idea of a general architecture: we had a good idea of what this thing looked like deployed, but what we had to figure out was what it looked like stowed, and how it went from stowed to deployed” said Flynn.
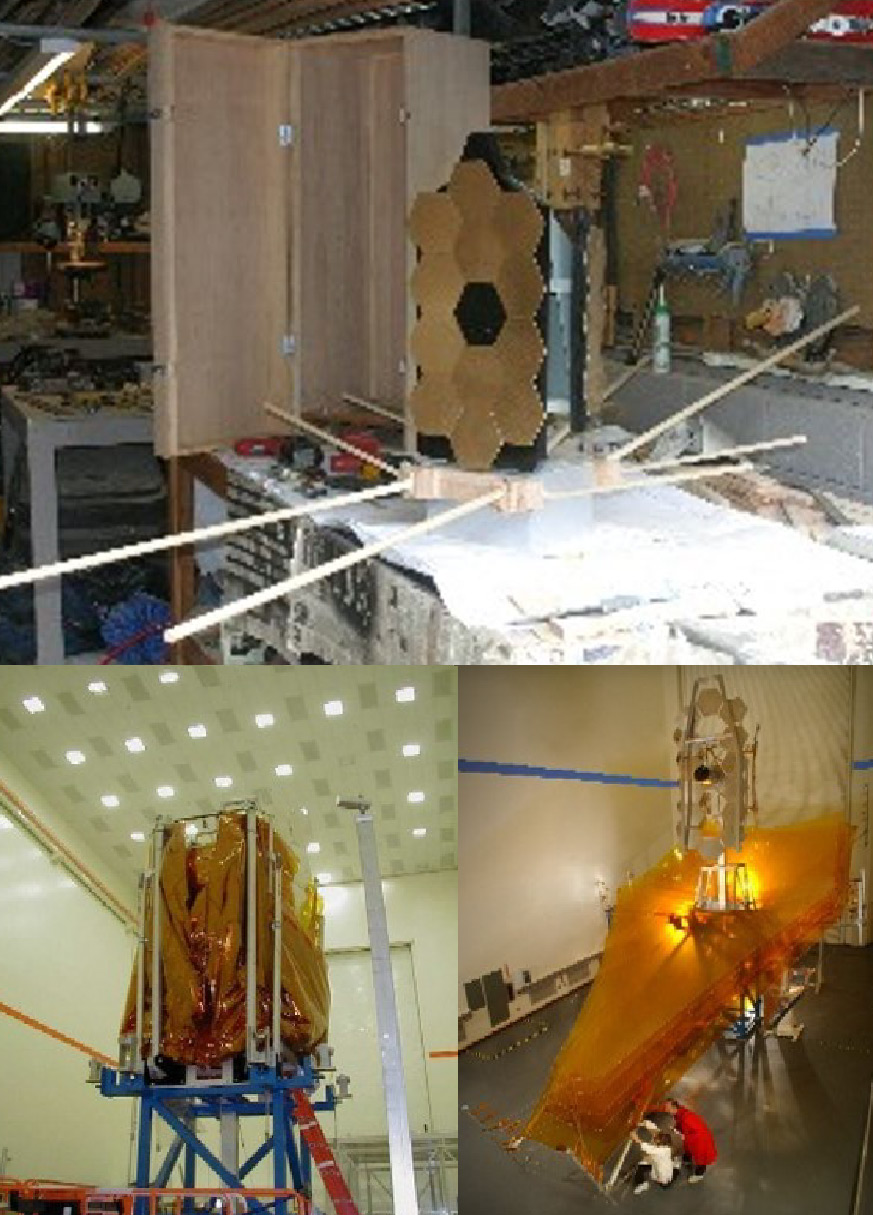
Original Concepts
The original concept used a total of eight deployable booms, Flynn said, with a set of two booms protruding from each side of the spacecraft, which would support the tensioned sunshield.
“Even back then, we knew the sun shield had five layers, we knew the general size,” he continued. “But getting it stowed safely inside the launch vehicle and how it deployed from that configuration: that evolved over a number of iterations and a number of years.”
The sunshield's design lead at the time, John Bobco, spent a month of 2004 in his shop working on a 1/10th-scale working model made from wood and using plastic for the membrane layers, Flynn recalled.
Bobco found that the structure worked for the deployed system but when it came to stowing it for launch, it became unworkable, Flynn said.
“He came back to us with the model and said ‘Alright, now if you lift all these eight booms together, you can see what a mess this is going to be, right?’” Flynn recalled.
So, the team went back to the drawing board, bounced around ideas, and ultimately settled on a membrane stowage concept that originated with one of NASA's engineers. The design called for the sunshield to stow in z-shaped folds along two straight-line, parallel edges, sitting atop forward and aft pallets attached to Webb’s spacecraft bus.
The sunshield membranes would be unfolded by telescoping booms on either side of the bus, separated by spreader bars and tensioned with motorized cables, ultimately forming a giant, five-layered kite of progressively smaller layers.
Another big unknown for the team was: What would be the optimal shape of the sunshield?
“We spent a lot of time on that: What does the shape of the membranes need to be so that you get optimal thermal performance?” Flynn recalled. “How much can they sag or wrinkle and still be good?”
The original design for the sunshield used scalloped (or curved) edges across the five layers but an analysis showed that wouldn’t work. If the layers had scalloped edges, it would allow heat radiating up from the lower layers of the sunshield to reach the primary mirror, warming it up to unacceptable temperatures. The analysis showed the edges needed to be straight.
Fixing it meant the final sunshield needed to be more complicated, Flynn said.
"It added a lot of design complexity because now in every corner instead of pulling at one place we needed to be pulling in three directions: one in the middle to get the tension and two on the edges to get them straightened out,” Flynn recalled. “So, we went from 30 pull points to 90 pull points because now each edge has got three full points instead of one.”

To hammer out the overall architecture, test articles were progressively scaled up in size and complexity from a one-third-scale model, all the way up to the “independent verification article,” or IVA, which was a full-scale model.
By mid-2010, Flynn and the team felt good about the size, shape and performance of the sunshield based on the one-third scale model built in collaboration with membrane manufacturer Nexolve in Huntsville, Alabama.
“To verify deployed thermal performance, we had to do the testing on the third-scale instead of the full-size model because we couldn't build a thermal chamber the size of a tennis court and achieve the temperatures we needed,” Flynn said. “For the third-scale test article, we placed heaters on the bottom side, to simulate the sun, we measured the temperatures and compared the results to our thermal model predictions.
“And, actually, the test article did a little better than the thermal models predicted, which is kind of what you hope for.”
Layers of Complexity
Another key consideration in the sunshield architecture was the getting it to survive the launch.
“A launch vehicle is essentially a controlled explosion,” recalled Amy Lo, a senior engineer on the program since 2013. “It is very loud, there's a lot of shaking – a bunch of stuff is happening.
Achieving the correct shape for the sunshield with its straight edges had already added a lot of complexity to the sunshield but ensuring Webb could survive launch and open in a steady, controlled manner while evading snags would push Webb’s engineers to new levels of complication.
The question the sunshield team had to tackle as it advanced its design was: How could Webb be stowed securely to ensure that during launch it didn’t rip itself apart or break one or more of the motorized tensioning components needed to deploy the sunshield in space? Then, once it arrived in space, how could the sunshield deploy in a controlled way, avoiding snags or tears?
The answers, as the design matured, added a good deal of complexity, said Levi, the integration engineer. “It’s very hard to manage those membranes such that it’s as static as possible during launch and tightly controlled during deployment and in tensioning,” Levi said. “And as the design matured, what we discovered is we needed more membrane management features for both launch and deployment. So, over time, what that meant is they had to keep iterating and extending the system to increase the degree of control.”

Insane in the Membranes
Controlling the membranes for launch and during deployment required 107 membrane release devices that could be individually triggered to both hold the sunshield steady during launch and give operators maximum control while they deployed it in space. Each of the 107 membrane release devices turned into single-point failures: if they didn’t work, it could mean mission failure for NASA’s flagship observatory.
Venting the excess air from the sunshield was another challenge – and one that posed a lot of issues for the Northrop Grumman sunshield team.
Any air trapped between its five folded layers needed to be vented within the first 180 seconds of Webb’s launch so that when the observatory arrived in space, the trapped air wouldn’t damage the membranes or trigger a snag during deployment if escaping air caused the membranes to billow.
This required that the folded membrane system include venting features as well and design features to manage (or minimize) membrane billowing.
The billowing problem caused so much concern that the team had vent test chambers specifically modified to perform full-scale sunshield subsystem tests. Those tests showed that the venting features built into the system, as well as the membrane release devices, would minimize billowing and avoid damage, but it was yet another layer of complexity to navigate as the design advanced.
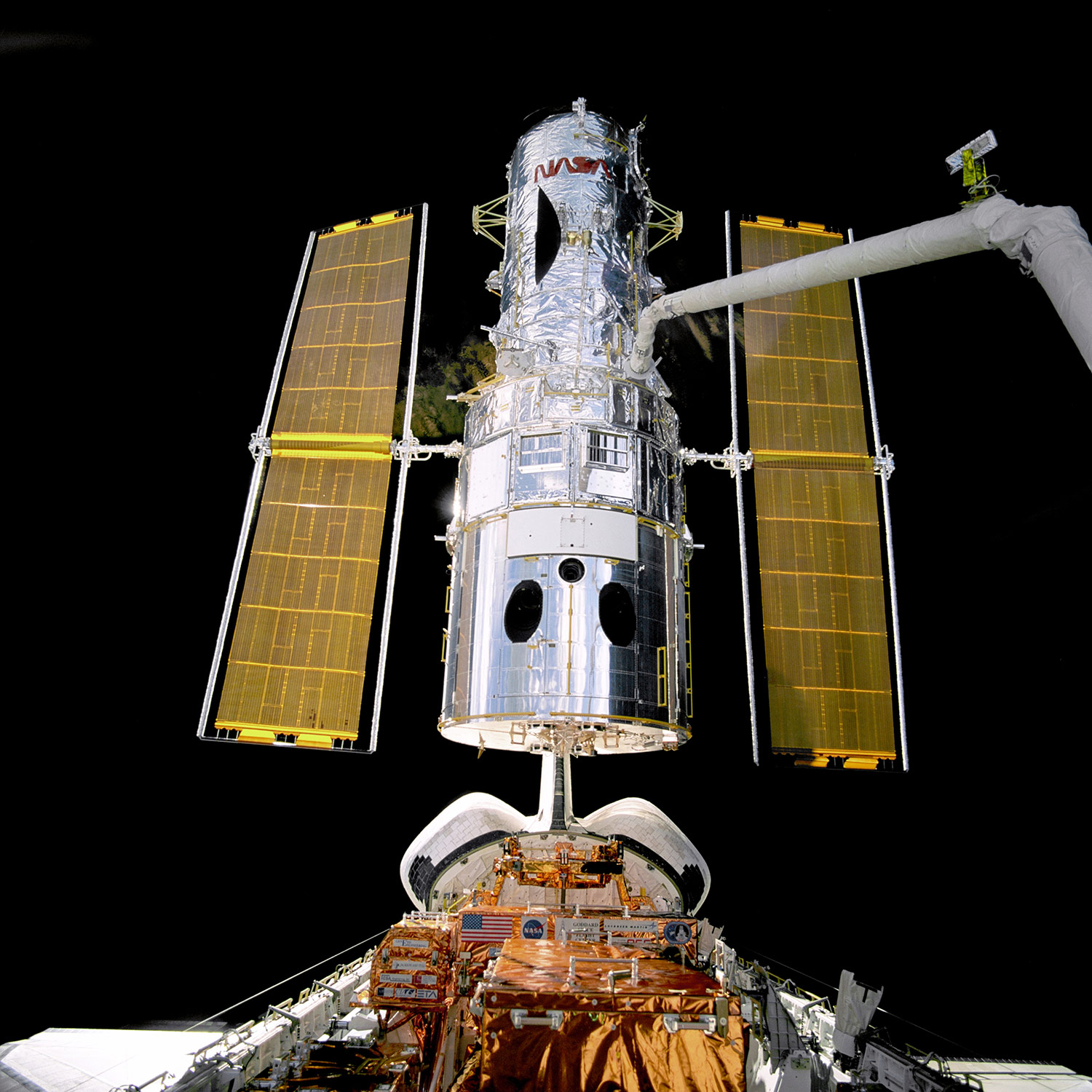
One Shot
Engineers, as a rule, try and make things as simple as possible. The Hubble Space Telescope (pictured) uses a monolithic mirror and the relative lack of moving pieces made it much simpler. It also constrained the capabilities of the telescope.
Webb was a different animal all together.
To meet Webb’s requirements and pave the way for ever-more power telescopes in the future, NASA and Northrop Grumman needed to design an observatory that only had one shot to deploy correctly after leaving its rocket fairing. Then it would make a million-miles journey to L2, well beyond the range of a manned rescue mission. For that kind of mission, engineers would want as few things as possible in the design that could go wrong and lead to failure.
As the program moved along, Flynn’s sunshield team grew and by time Webb had its mission critical design review in 2010, it was clear to everyone that the sunshield was going to be even more complicated than originally anticipated. By the time it neared its flight configuration, the observatory had acquired an anxiety-inducing 344 single-point failures, 295 of which were associated with deployments. And many of them lived in the sunshield design.
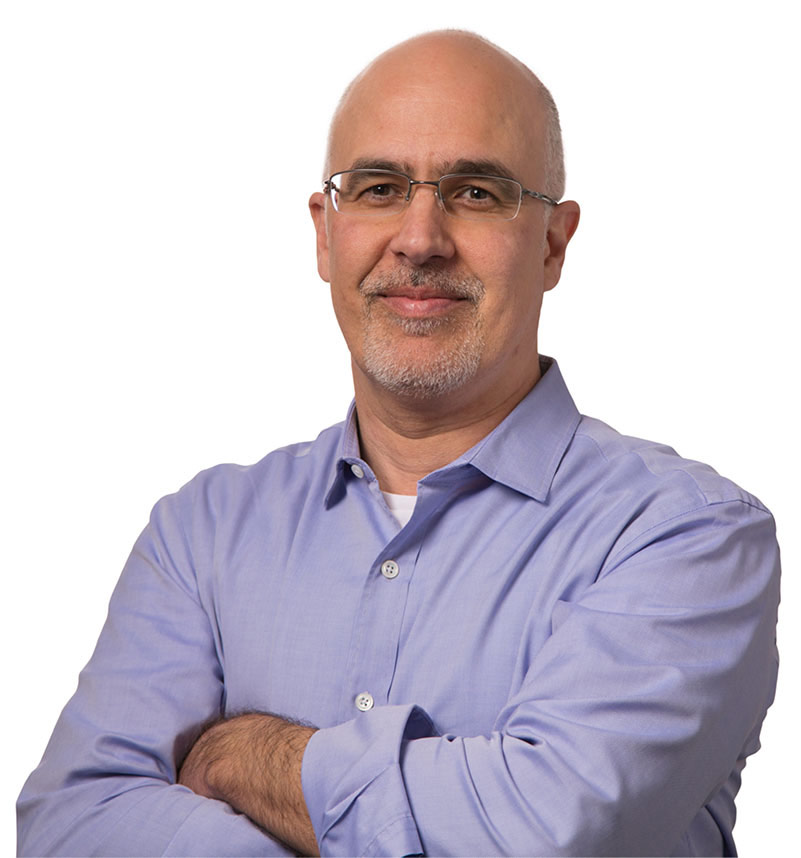
At every step of the way, though, the sunshield team drove down risk and eliminated all possible complexity through revisions and ever-higher fidelity test articles, Flynn said. The team also put each individual mechanism and subsystem through individual testing to make sure it would perform on orbit.
And the complexity was unavoidable, said Scott Willoughby (pictured), Northrop Grumman’s program manager for Webb. Every test and external review validated Northrop Grumman’s engineering of the sunshield, he said.
“The membranes at one point required 109 release devices and we worked our tails off just to get it down to 107,” Willoughby said. “We didn’t drink our own bathwater here: We had independent reviewers come in – I remember one from the National Academies came in and spent a week looking over our work. At the end of it he said: ‘You're doing it right; you’re doing everything that I would do. It’s just hard and it scares the hell out of me.’”

The Final Stretch Begins
With a mature design in hand and the team confident it was coalescing around the right system, the final pieces of the Webb puzzle started coming together. The spacecraft bus passed its critical design review in 2014 – a crucial final step toward integration of the sunshield on to the observatory.
Flynn’s sunshield team that started out with four people, was growing all the time and would eventually number more than 100 people.
And with final integration and testing, more challenges appeared.
"Webb is a Swiss watch movement," Willoughby said. "And just like a Swiss watch, every piece of it depends on every other component. So, if your gear is turned by another watchmaker's hairspring and balance assembly, you have to wait for that piece to know exactly how and where to install your gear, and it's not possible to anticipate all the things that might change or need to be accounted for until you start putting it all together."
Integrating and testing Webb revealed new surprises and changes that made the system better, but to Willoughby’s mind, it’s hard to think of any way it could have gone differently.
“Webb was always constrained by its own reality: It’s too big and too novel to ever do anything without doing it for the first time,” Willoughby said. “And that first time was sometimes later than you’d want because you’re building a massively complicated bus and a massively complicated sunshield that naturally live their own lives separately for a long time before coming together. …
“When the day came where we had a put a sunshield on a bus for the first time, it was more than 10 years from the program's start. And we learned a lot of lessons.”