Next-Generation Scramjet Delivers Hypersonic Propulsion That Weighs Less to Pack More Punch
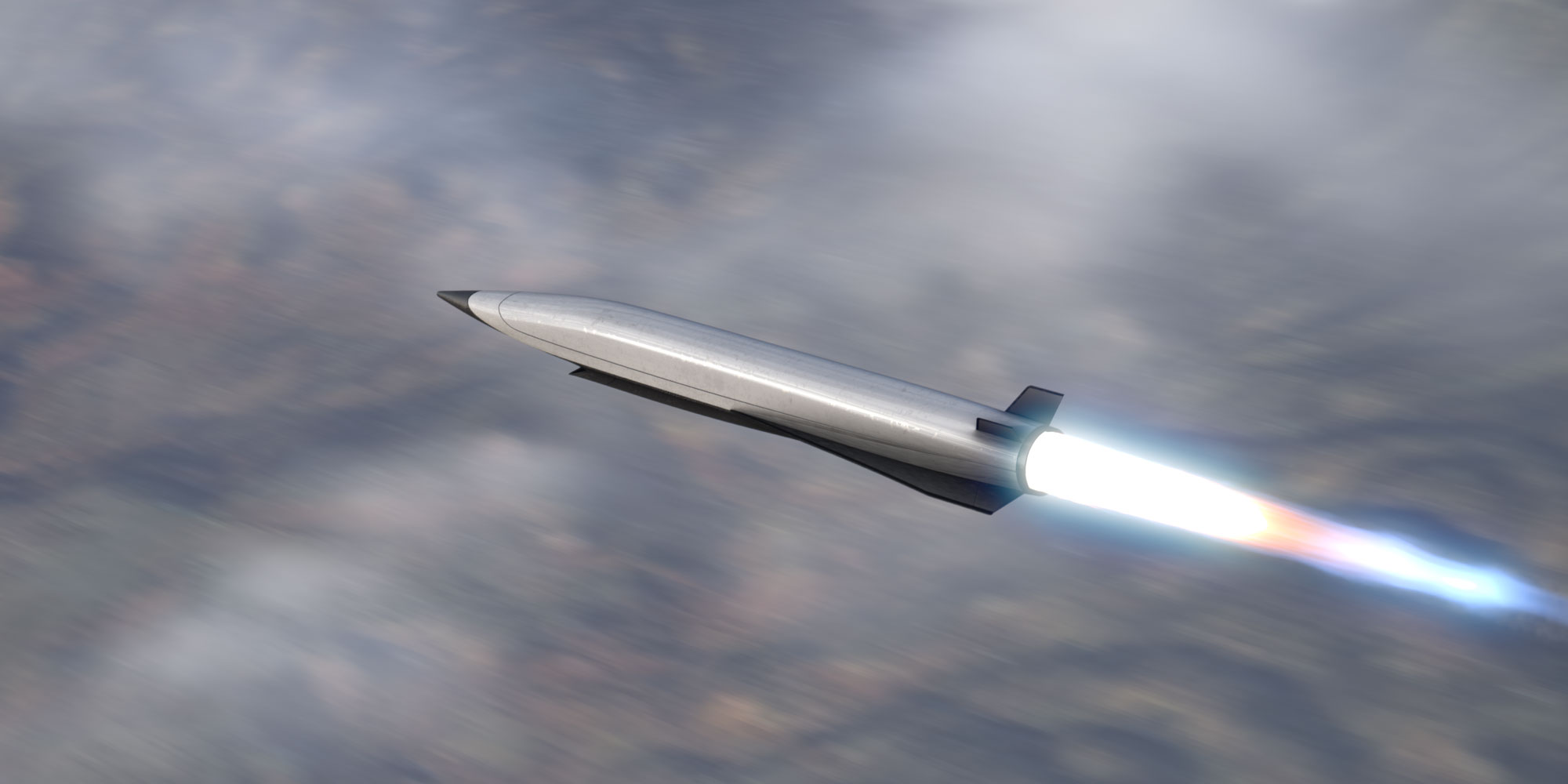
By Kenneth Kesner
Speed and stealth are key in the all-domain battlespace. A hypersonic pace – five or more times the speed of sound – can put a missile on target before enemy defense systems can respond effectively. Having long range hypersonic systems allows pilots to prosecute targets without having to put themselves within range of air defense systems.
Dependent on the mission need, scramjet propulsion systems are capable of achieving hypersonic speeds in an optimized package for a long range, time-critical strike capability. The need for extended ranges while maintaining magazine depth really plays to the strengths of hypersonic air-breathing propulsion. Air-breathing engines leverage the oxygen in the atmosphere and minimal moving parts to deliver a high speed weapon systems in a tactical form factor. The result is a great number of weapons on the platform which gives our warfighters the flexibility and operational utility they need in a near-peer fight.
What military strategists want is a missile that combines speed, range, high load out, and affordability.
Game, set, match. Northrop Grumman’s next-generation scramjet engine helps solve those challenges. It has already propelled a Hypersonic Air-breathing Weapons Concept (HAWC) missile through milestone flight tests for the Defense Advanced Research Projects Agency and the U.S. Air Force (USAF), most recently in summer of 2022, with more tests to come. HAWC was developed by Raytheon Missiles & Defense, a Raytheon Technologies business, in partnership with Northrop Grumman. The partnership team was recently selected to develop the USAF’s Hypersonic Attack Cruise Missile (HACM) – a first-of-its-kind weapon being developed in conjunction with the Southern Cross Integrated Flight Research Experiment (SCIFiRE), a U.S. and Australia project arrangement.
Scramjets have been studied since the late 1950s, with few sustained flight successes. They are essentially supersonic ramjet engines and require high vehicle speed – provided by a rocket booster or supersonic aircraft – to compress air through an inlet into a combustion chamber. That’s where oxygen combines with fuel and is ignited, creating the tremendous thrust that enables sustained hypersonic flight.